Our Quality Control Process For Custom Clothing
Our Commitment To High-quality Clothing Delivered
Quality is the cornerstone of everything we do.
We take pride in delivering custom clothing that meets high-quality standard.
Steps in Quality Control
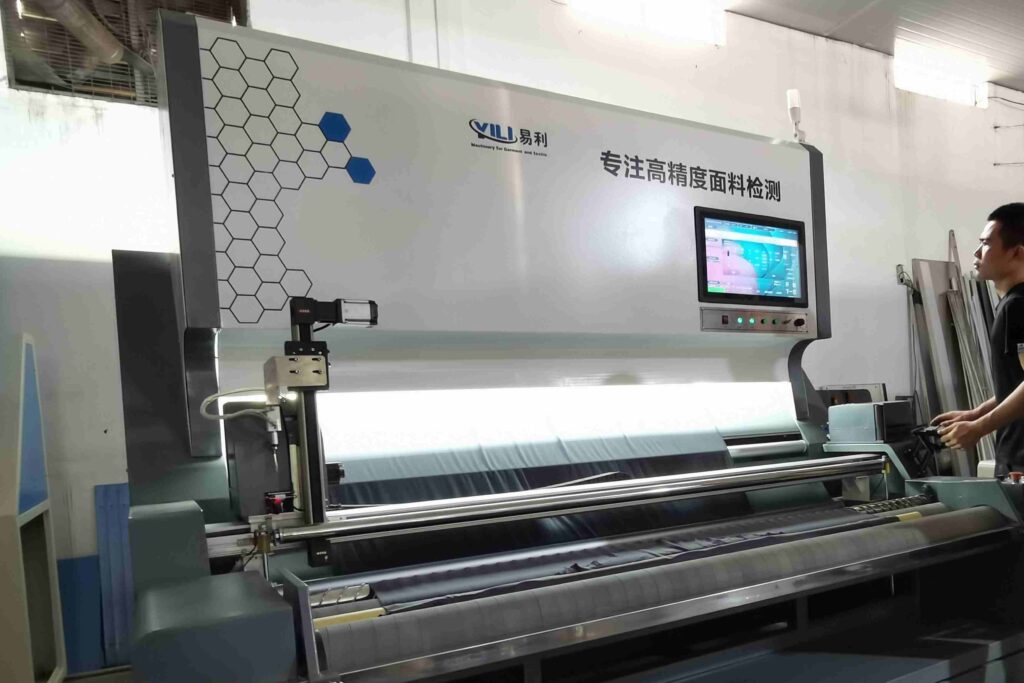
Material Inspection
Ensuring Quality from the Start
Pre-Production Quality Control
Laying the Foundation for satisfaction
Pre-production quality control is a vital step to ensure your garments meet exact specifications from the start. We will make at least one piece of each size for initial inspection. Based on the designs and samples approved by customers, we carefully inspect raw materials, confirm design details, and verify production setups to prevent errors. If any issues are identified, immediate adjustments will be made to the production process to address and resolve potential problems at their root. This proactive approach guarantees consistent quality and smooth production, delivering satisfactory results.
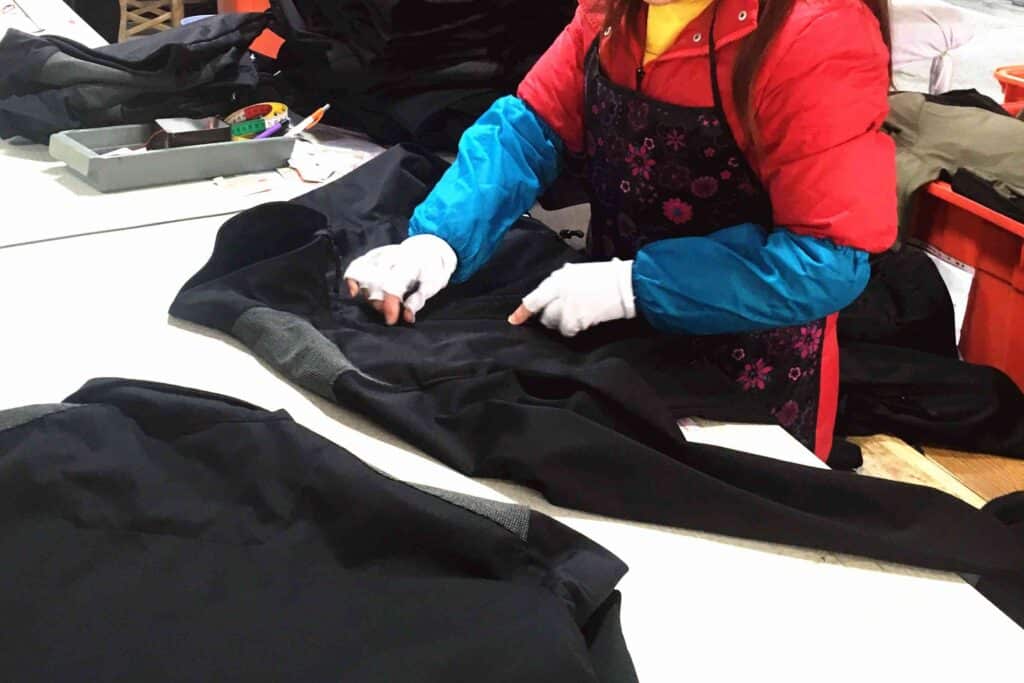
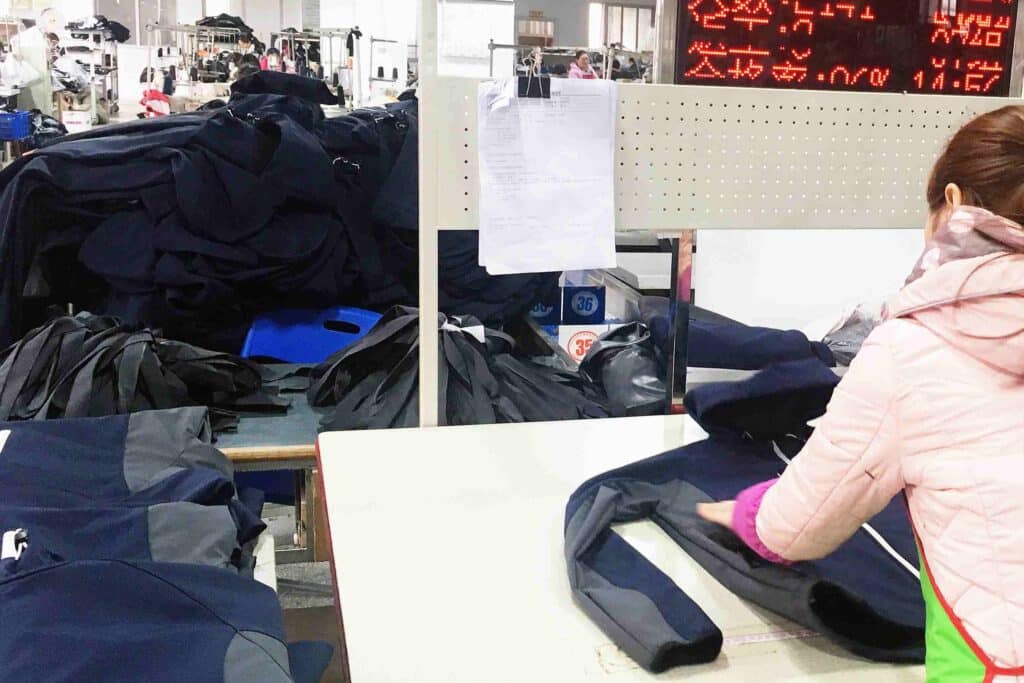
On-Line Process Inspection
Ensuring Excellence at Every Step
Finished Products Inspection
Guaranteeing Perfection
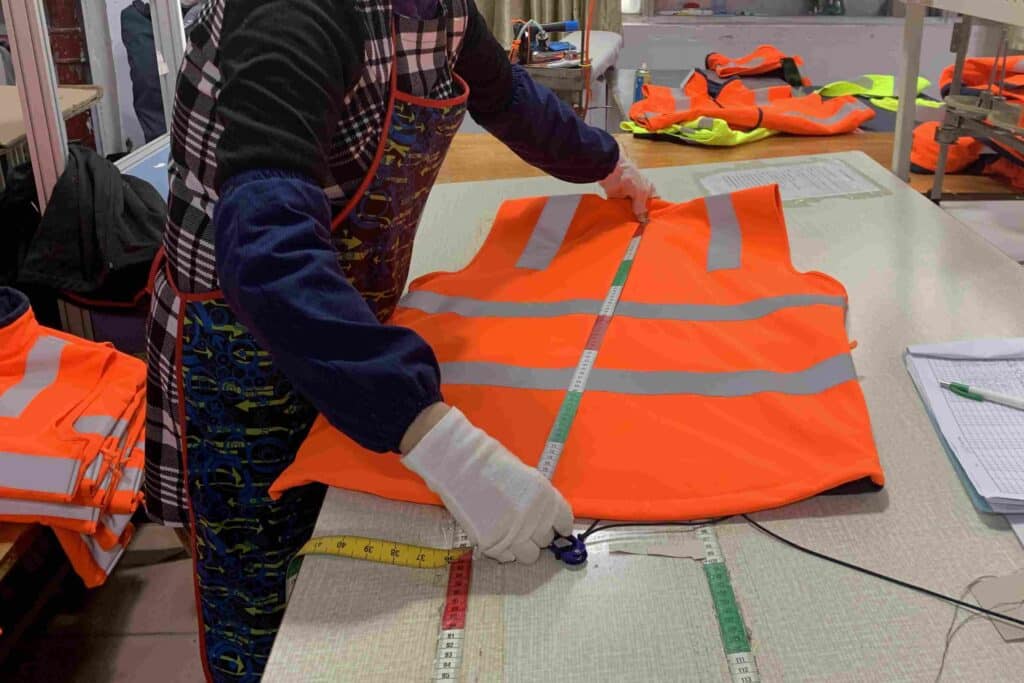
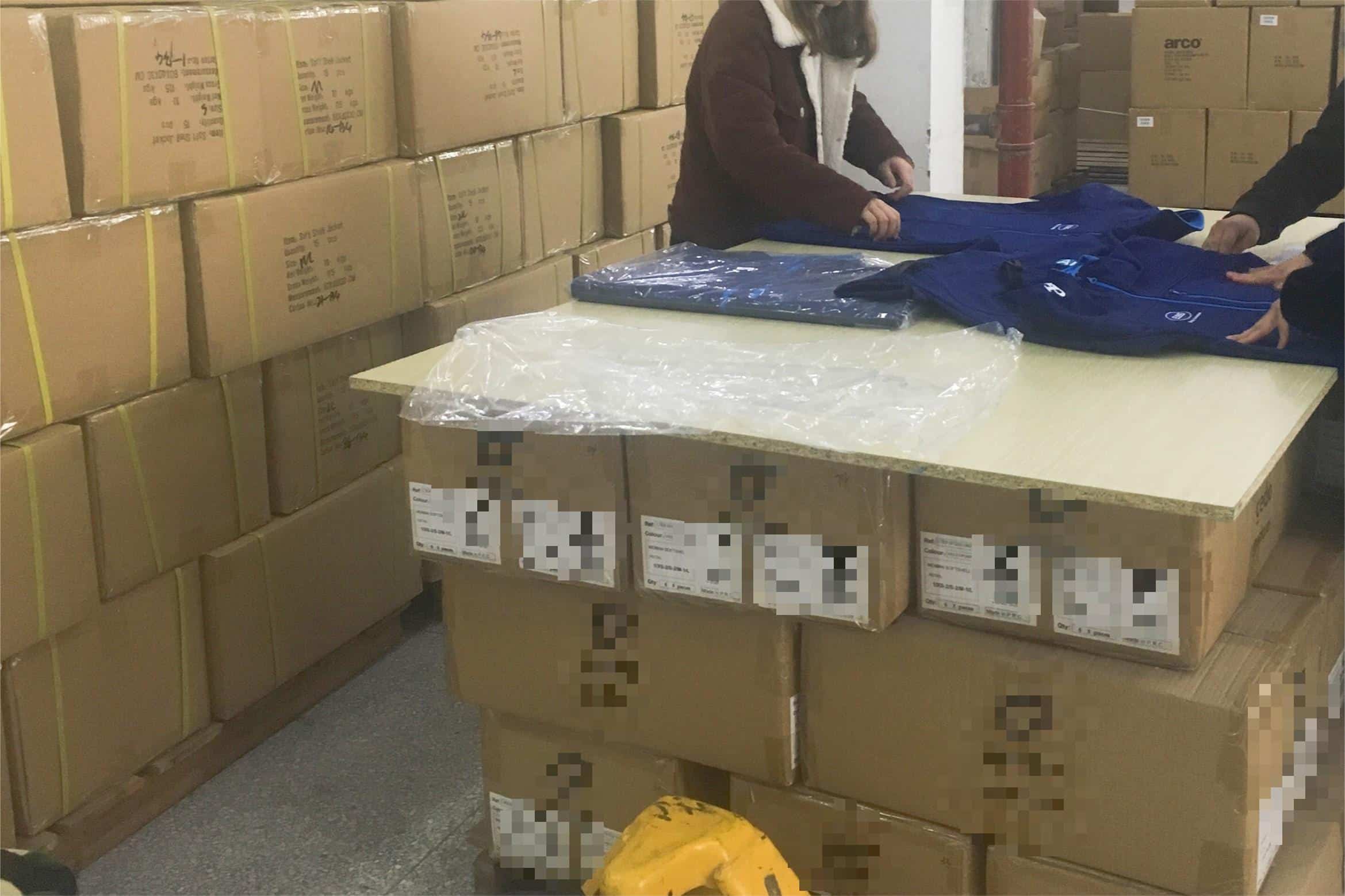
Work With Independent Inspection
Ensuring Unbiased Quality Assurance
Client Involvement in Quality Control
We believe in transparency and collaboration. We encourage our customers to actively participate in the quality control process to ensure their expectations are fully met. From reviewing and approving fabric samples, colors, and designs before production, to monitoring key production stages and even arranging third-party inspections, your involvement helps us align every detail with your requirements. By keeping you informed and engaged, we deliver garments that perfectly reflect your brand’s standards and vision.
Pre-Production Samples
Virtual or In-Person Inspections
Customized Checklists
Regular Updates
Feedback-Driven Improvements
Let's Work Together To Ensure Perfect Custom Clothing Delivered
Testing Methods
Fabric Quality Inspection
Ensuring Excellence from the Start
Fabric quality is the foundation of every exceptional garment. At Identity Custom Clothing, we take rigorous steps to ensure that every piece of fabric used in our production meets the standards of durability, comfort, and appearance. From selecting premium materials to conducting thorough inspections for colorfastness, texture, and strength, our meticulous fabric quality control process guarantees that your clothing not only looks great but also stands the test of time. By prioritizing fabric excellence, we ensure that every product reflects your brand’s commitment to quality.
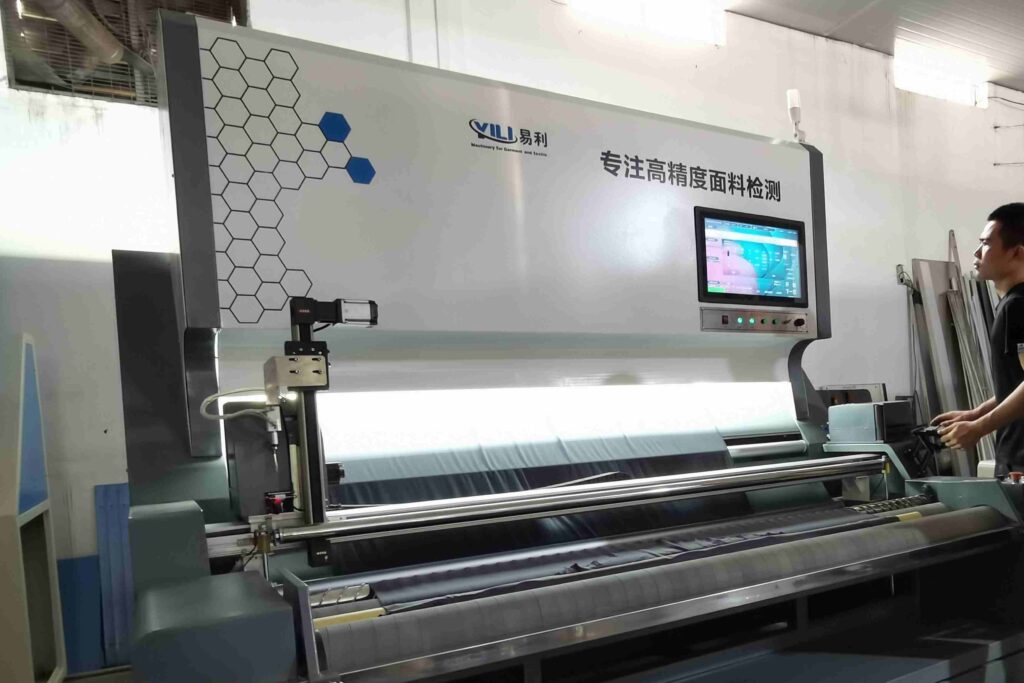
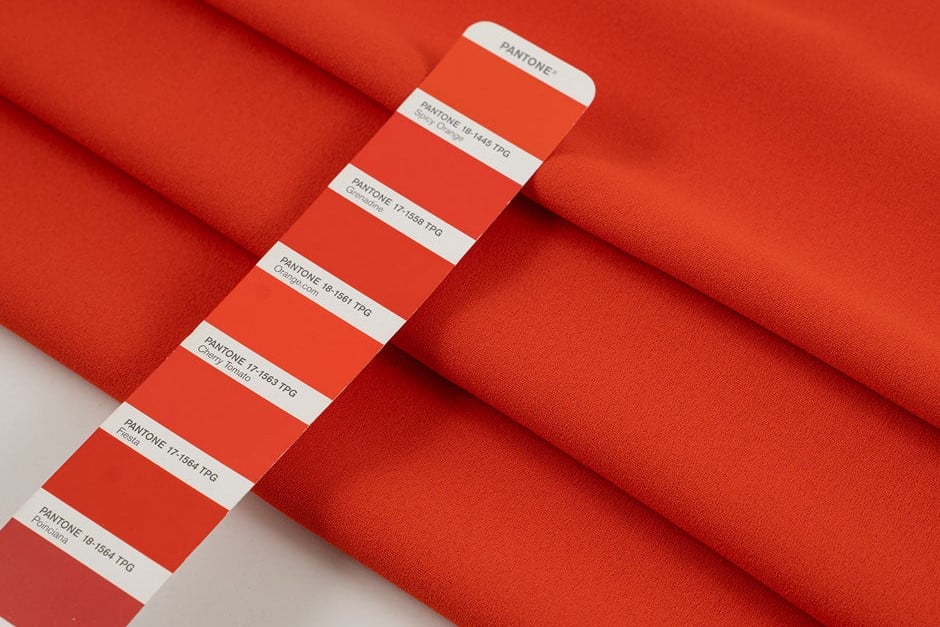
Color Identification
Precision Matching for Your Brand
Color Fastness Test
Preserving Vibrancy & Quality
Color fastness is critical to maintaining the long-lasting vibrancy and professional appearance of your garments. At Identity Custom Clothing, our fabric color fastness inspection process ensures that colors remain true and resistant to fading, bleeding, or discoloration over time. Through rigorous testing under various conditions such as washing, exposure to light, and rubbing, we verify that each fabric meets the standards for durability and consistency. This commitment ensures your custom clothing retains its brilliance, perfectly representing your brand with every wear.
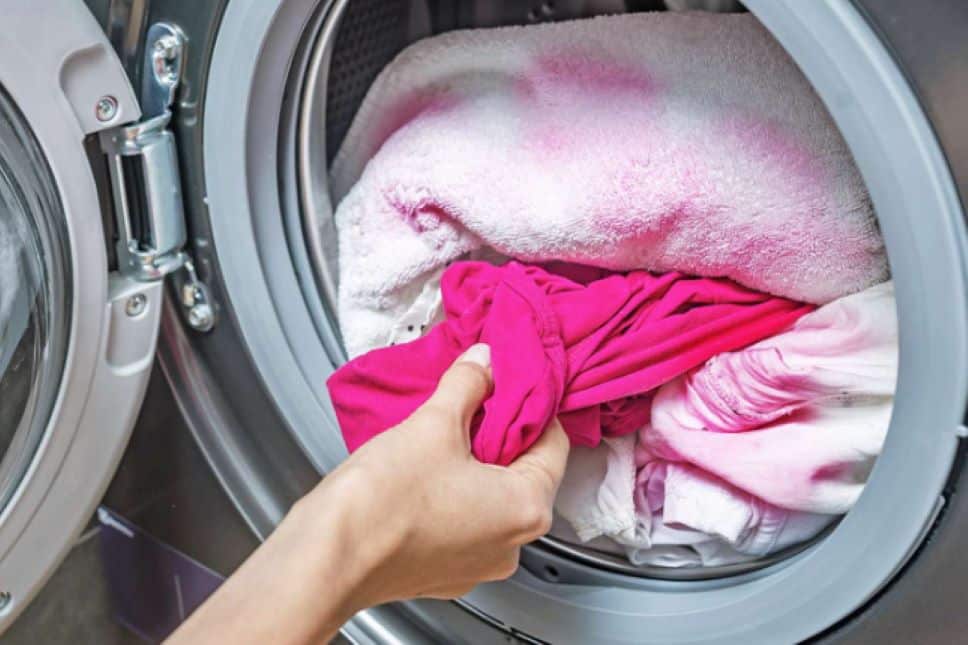
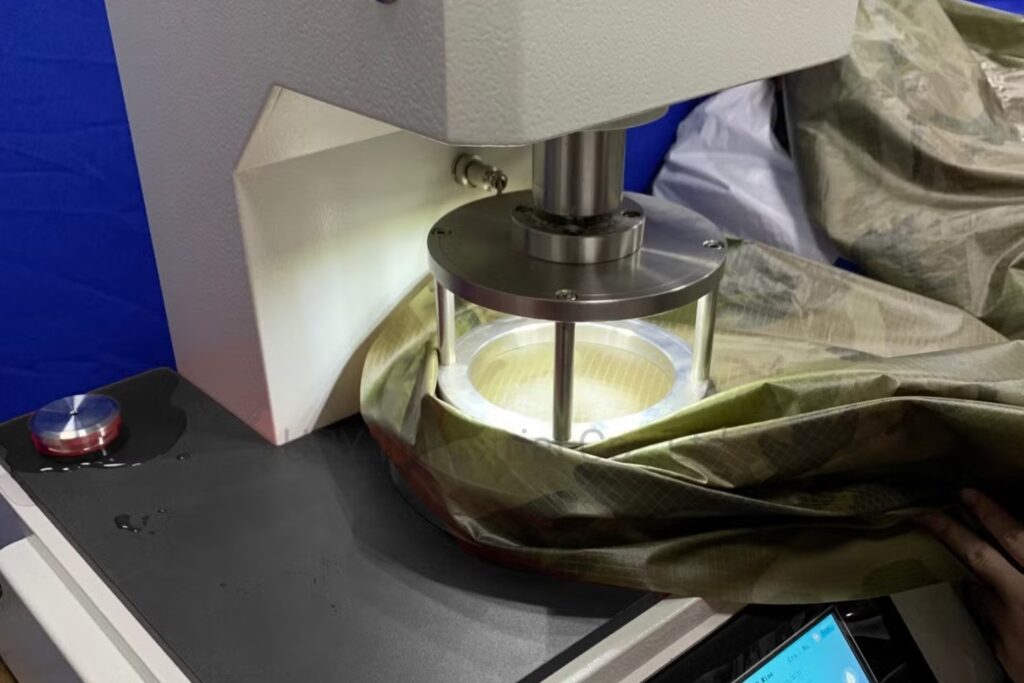
Fabric Water Pressue Test
Ensuring Waterproof Performance
Tear & Break Strength Test
Ensuring Durability
Durability is key to high-quality outdoor garments, and our Tear & Break Strength Test ensures your products can withstand daily wear and demanding conditions. At Identity Custom Clothing, we rigorously evaluate fabrics to measure their resistance to tearing and breaking under stress. By using advanced testing methods, we ensure that every material meets the standards for strength and reliability. This commitment guarantees that your custom clothing delivers exceptional performance and long-lasting quality.
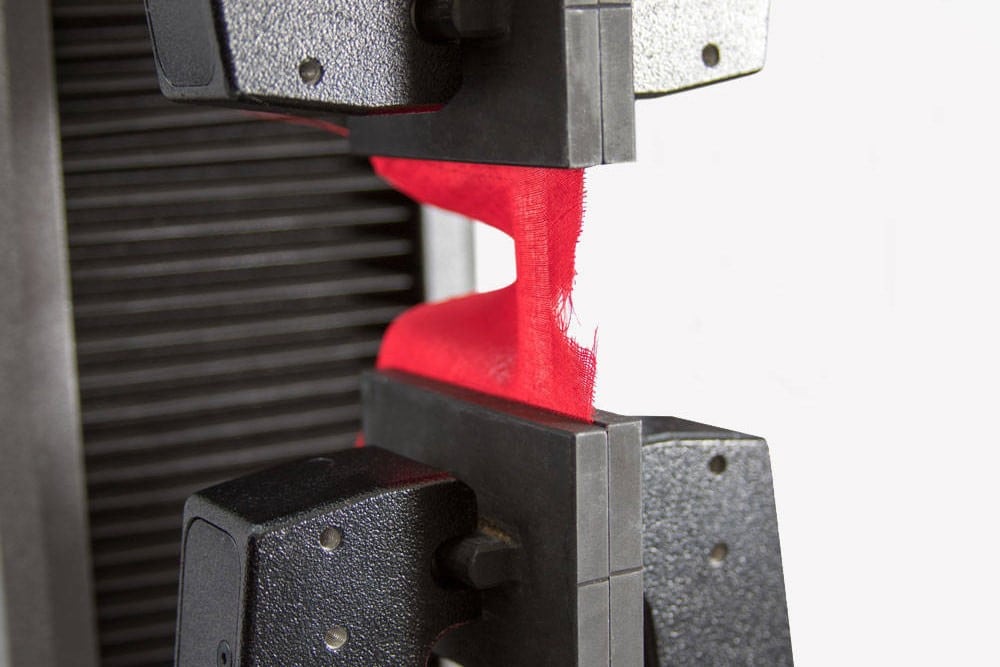
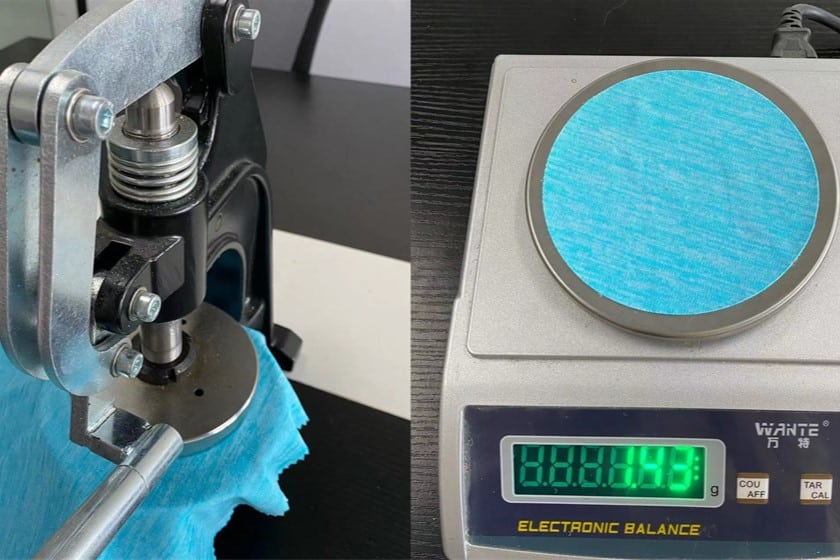
Fabric GSM Weight Test
Ensuring Quality & Consistency
At Identity Custom Clothing, we conduct precise GSM weight test to ensure each material meets your specific requirements for durability and functionality. By verifying the weight per square meter (GSM), we guarantee consistency and quality, helping determine its thickness and quality, tailoring fabrics to suit your needs, from lightweight wear to durable outdoor apparel.
Fabric Abrasion Resistance Test
Ensuring Longevity
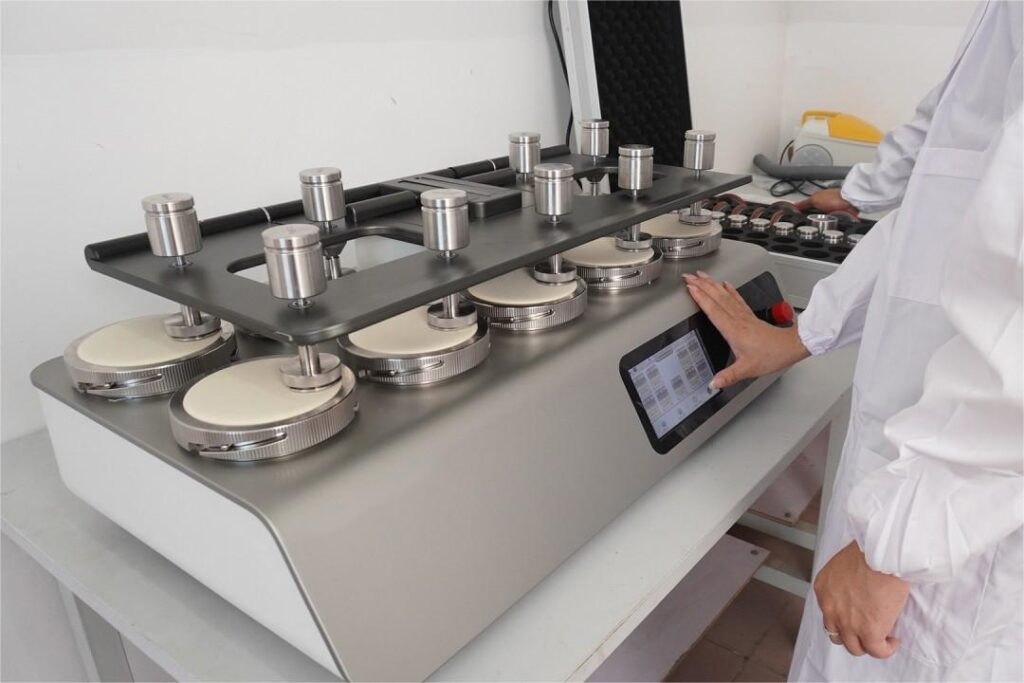
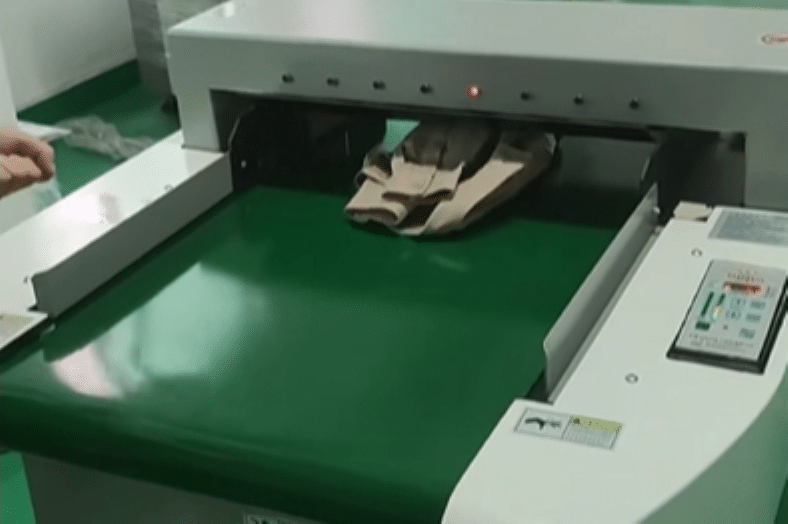